Zastosowanie pneumatycznej techniki pomiarowej w urządzeniach ortopedycznych
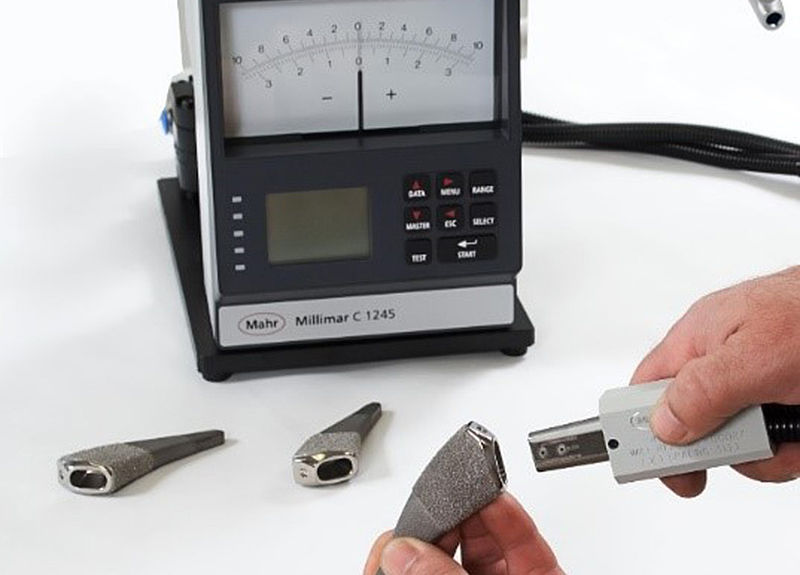
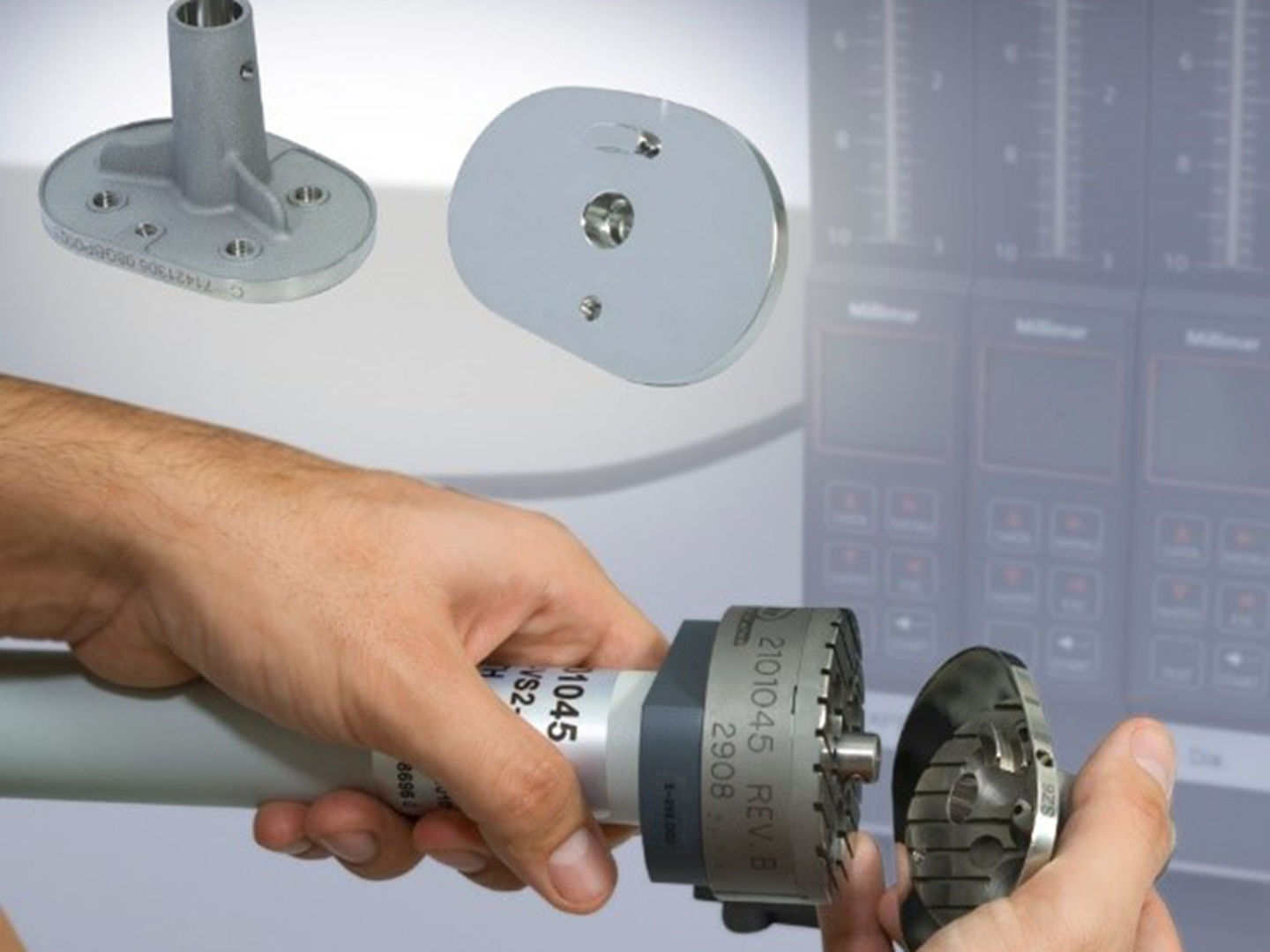
Ortopedyczne elementy precyzyjne mogą spełniać wysokie wymagania jakościowe tylko wtedy, gdy każdy etap produkcji (od pierwszego cięcia po obróbkę końcową) jest niezmiennie stabilny. Wymaga to zorientowanej na proces kontroli właściwości, natychmiastowej informacji zwrotnej w przypadku przekroczenia tolerancji oraz dokumentacji wszystkich danych procesowych.
Zazwyczaj, gdy obrabiane elementy przechodzą przez proces produkcyjny od surowca do gotowego produktu, tolerancja wymiarów, wykończenie powierzchni i cechy geometryczne stają się coraz bardziej krytyczne – co sprawia, że jeszcze bardziej krytyczne jest utrzymanie tych tolerancji lub rozpoznanie, kiedy zostały przekroczone. Jedną z cech wymiarowych mierzonych na końcu procesu produkcyjnego sprzętu ortopedycznego jest ścisła tolerancja na powierzchniach stożkowych w celu dopasowania poszczególnych części. Na przykład, większość implantów biodrowych i kolanowych wykorzystuje stożkowe powierzchnie dla optymalnego ustawienia i bezpiecznego „zablokowania” komponentów we właściwej pozycji. Już podczas produkcji tych części kontrola kształtu i wielkości stożka decyduje o tym, jak dobrze implanty ortopedyczne będą się sprawować przez cały okres ich użytkowania.
Dlaczego pneumatyczna technika pomiarowa jest najbardziej efektywną metodą?
Przy coraz bardziej wąskich tolerancjach, sprawdziany muszą być coraz bardziej wytrzymałe i posiadać odpowiednie cechy konstrukcyjne, aby zapewnić prawidłowe zamocowanie części. Muszą one również posiadać rozdzielczość i dokładność odpowiednią do pomiaru wymaganych tolerancji. Pneumatyczna technologia pomiarowa coraz częściej staje się preferowanym rozwiązaniem testowym do sprawdzania tych krytycznych parametrów. Pneumatyczne urządzenia pomiarowe są niezwykle precyzyjne i oferują bardzo wysoką rozdzielczość. Są one zwykle stosowane w aplikacjach, w których tolerancje są wąskie – zwykle poniżej ± 25 µm – a chropowatość powierzchni jest mniejsza niż Rz 6,3 µm. W takich warunkach, jak w przypadku precyzyjnych stożków do zastosowań medycznych, pneumatyczna technika pomiarowa jest często najlepszym rozwiązaniem.
Pomiary pneumatyczne są również szczególnie odpowiednie do sprawdzania proporcji wymiarowych; pneumatyczne urządzenia pomiarowe są szybkie, łatwe w obsłudze i mają wieloletnią żywotność, nawet w najtrudniejszych warunkach pracy w produkcji – pozwala to zmierzyć miliony części. W niektórych przypadkach metrologia pneumatyczna może być nawet stosowana do kontroli i oceny określonych cech kształtu części.
Dysza pomiarowa, czyli mały otwór, z którego wydobywa się powietrze, jest powodem, dla którego pneumatyczna technika pomiarowa jest tak przydatna do pomiaru powierzchni stożków ortopedycznych. Żaden inny czujnik pomiarowy nie jest tak mały i nie może być umieszczony tak blisko punktu pomiarowego, gdy do zmierzenia jest wiele średnic lub kształtów geometrycznych. Małe czujniki elektroniczne lub czujniki wiroprądowe mogą zbliżyć się do wielkości dyszy pomiarowej, ale nie dorównują jej pod względem ekonomiczności i przydatności do bezpośredniego zastosowania w produkcji na hali produkcyjnej.
Możliwy jest pomiar średnic i stożków za pomocą kombinacji czujników elektronicznych lub współrzędnościowej maszyny pomiarowej z sondami krawędziowymi. Dysza pomiarowa może być zainstalowana bezpośrednio w urządzeniu precyzyjnym, dzięki czemu można ją wykorzystać do pomiaru części bezpośrednio w produkcji. W ten sposób pomiar może być wykonany w jednym szybkim procesie, przy minimalnym wysiłku operatora. Ani współrzędnościowe maszyny pomiarowe, ani metrologia optyczna nie oferują szybkości i dokładności wymaganej do osiągnięcia stuprocentowej kontroli przedmiotów obrabianych na hali produkcyjnej i zapewnienia natychmiastowej informacji zwrotnej na temat wydajności procesu.
Wybór właściwego sprzętu pomiarowego
W praktyce jest tyle metod definiowania wymagań dotyczących stożka, ilu jest producentów elementów stożkowych. Obszar odniesienia może się różnić w zależności od producenta, a tolerancje mogą być podane w różny sposób.
W zależności od sposobu połączenia części w całość, tolerancje dla stożka mogą być bardziej rygorystyczne niż dla średnicy lub odwrotnie. Alternatywnie, kombinacja tolerancji stożka może być określona tylko dla jednej średnicy. Dlatego też oznaczenie na rysunku jest najlepszą wskazówką przy wyborze odpowiedniej wersji pneumatycznego urządzenia pomiarowego. W metrologii pneumatycznej przyrządy kontrolne są wykonywane na zamówienie dla każdego zastosowania stożka, dlatego istotne jest, aby rozważyć wymagania w odniesieniu do konkretnego przedmiotu obrabianego. Niemniej jednak, elastyczność i zalety tej metody pomiarowej są prawie nie do przebicia: oferuje ona bardzo wysoką rozdzielczość, a czujniki pomiarowe mogą być wielokrotnie łączone w celu uzyskania dowolnej liczby wymiarowych i geometrycznych danych pomiarowych bezpośrednio na produkcji.
Różne typy pneumatycznych sprawdzianów stożkowych
Implanty medyczne muszą być wyjątkowo trwałe i odporne, dlatego też stożkowe dopasowanie pomiędzy matrycą a patrycą musi być bardzo precyzyjne. Obie części muszą być pewnie połączone i znajdować się na właściwej wysokości. Podczas produkcji powszechną praktyką jest testowanie 100 procent części, aby zapewnić dokładność wykonania obu elementów. Zazwyczaj jest to wykonywane przy użyciu pneumatycznej techniki pomiarowej, która łączy w sobie niezbędną wysoką rozdzielczość i dokładność z szybkością, łatwością obsługi i wytrzymałością wymaganą w sektorze produkcyjnym.
Najbardziej rozpowszechniony typ pneumatycznego sprawdzianu stożkowego posiada dwie pary dysz w dwóch płaszczyznach pomiarowych i jest przeznaczony do systemu płaszczowego między przedmiotem obrabianym a sprawdzianem (patrz ilustracje). Jeśli kąt stożka jest zbyt duży, na mniejszym końcu stożka występuje większy luz pomiędzy obiema powierzchniami. Jeśli kąt stożka jest zbyt mały, na większym końcu występuje większy luz. W obu przypadkach może to doprowadzić do zmniejszenia dopasowania kształtowego połączenia, co z czasem może spowodować utratę „bezpiecznego połączenia” poprzez poluzowanie lub przekręcenie. Jeśli kąt stożka jest prawidłowy, ale rozmiar jest niewłaściwy, prowadzi to do nieprawidłowej długości całkowitej jednostki ortopedycznej, a tym samym do nieoczekiwanych rezultatów po implantacji.
W przypadku trzpieni pomiarowych do dysz stożkowych z systemem płaszczowym nie mierzy się średnic cząstkowych, lecz wskazuje różnicę średnic w dwóch punktach pomiarowych na elemencie mierzonym, które są następnie porównywane z odpowiednimi punktami pomiarowymi wzorca lub matrycy. Jeśli różnica średnic na dużym końcu stożka jest większa niż różnica średnic na małym końcu, górne dysze będą wykrywały większe ciśnienie wsteczne niż dysze dolne. W tym przypadku oznacza to stożek ujemny lub większy kąt stożka. Jeżeli różnica średnic na małym końcu jest większa, to sytuacja jest odwrotna i na urządzeniu pomiarowym można odczytać stożek dodatni. Jednakże, ponieważ pneumatyczny sprawdzian stożkowy z osłoną wskazuje jedynie różnice średnic, nie wskaże on częściowej średnicy w obu punktach. Tak więc, chociaż ten typ pneumatycznego urządzenia pomiarowego dostarcza dobrych informacji na temat zużycia stożka pomiarowego i pozwala przewidzieć dopasowanie kształtu połączenia, nie może jednak dostarczyć informacji na temat dokładności pozycjonowania elementów stożka.
W tym celu stosuje się pneumatyczne urządzenie pomiarowe ze stykiem czołowym (czasami określane również jako konstrukcja kołnierzowa), w którym pierścieniowy zbiornik do pneumatycznego pomiaru stożka jest tak zwymiarowany, że może pomieścić cały stożek. W zależności od tego, gdzie znajduje się powierzchnia odniesienia części, część może mieć odniesienie do końca stożka lub do kołnierza (ramienia) przy górnej powierzchni części. Umożliwia to pomiar średnic na znanych wysokościach (oprócz odchyłki luzu, jak w przypadku wersji z systemem płaszczowym). Dodatkowy poziom dysz pomiarowych może być dodany w celu zbadania wklęsłego lub wypukłego kształtu cylindrycznego – są to dwa dodatkowe warunki, które zmniejszają powierzchnię styku pomiędzy oboma elementami pasowanymi (stożkiem wewnętrznym i zewnętrznym).
Trzeci typ pneumatycznego miernika stożkowego jest połączeniem poprzednio opisanych typów. Jest to zasadniczo pneumatyczne urządzenie pomiarowe z systemem płaszcza i czujnikiem pomiaru długości odniesionym do powierzchni odniesienia. Umożliwia to wyświetlanie głębokości zanurzenia pneumatycznego urządzenia pomiarowego w mierzonym elemencie. A zatem podczas gdy kąt stożka może być odczytany z pneumatycznego urządzenia analizującego, wyświetlacz czujnika pomiaru długości zapewnia wskazanie głębokości poszczególnych średnic. Podczas pomiaru przedmiotu za pomocą stożka wewnętrznego, jeśli pochylenie stożka jest zbyt duże, sprawdzian wejdzie głębiej w przedmiot. Jeśli nachylenie jest zbyt małe, nie wejdzie on w przedmiot tak daleko, jak się tego oczekuje. Jeśli głębokość zanurzenia jest określona za pomocą sondy pomiarowej, wartość ta może być użyta do obliczenia średnic na dowolnej głębokości pomiaru.
Uwzględnienie powierzchni
Ze względu na wysoką dokładność i rozdzielczość pneumatycznej techniki pomiarowej może mieć na to wpływ jakość powierzchni części. Prowadzi to do komplikacji w stosowaniu pneumatycznej techniki pomiarowej, ponieważ do jej użycia wymagana jest dobra powierzchnia. W normalnych warunkach użytkowania strumień powietrza z dysz pomiarowych pokrywa pewien obszar powierzchni części. Strumień powietrza jest odbijany od powierzchni w celu wytworzenia ciśnienia wstecznego wymaganego do pomiaru. Na gładkiej powierzchni różnica pomiędzy średnią powierzchnią a szczytami chropowatości, które w przypadku detalu o średnicy wewnętrznej są synonimem minimalnego luzu, jest raczej nieznaczna. Jeśli jednak powierzchnia jest bardzo chropowata, obszar lub punkt, w którym powstaje ciśnienie wsteczne, może się znacznie różnić. Może to zostać zarejestrowane na wyświetlaczu manometru pneumatycznego i wpłynąć na wyświetlaną średnicę.
Jeśli jednak wystąpią problemy z powierzchnią, można podjąć specjalne kroki w celu ich rozwiązania. Dopóki chropowatość powierzchni jest mniejsza niż Rz 6,3 µm, przesunięcie może być zwykle ignorowane. Ale nawet jeśli tak nie jest, błąd wykryty podczas projektowania procesu może zostać skompensowany, a rzeczywista średnica wyświetlona operatorowi maszyny. Ze względu na charakter stanu powierzchni i jej reakcji w przypadku dyszy pomiarowej z wolnym wydmuchem, elektroniczne wzmacniacze i komputery pomiarowe mogą również zapewnić wiarygodne obliczenia średnich lub maksymalnych średnic.
Wniosek
Precyzyjne komponenty ortopedyczne muszą niezawodnie spełniać bardzo wysokie wymagania jakościowe. Jedną z krytycznych cech mierzonych podczas procesu produkcyjnego jest ścisła tolerancja na powierzchniach stożkowych w celu dopasowania poszczególnych części. Przy coraz bardziej wąskich tolerancjach, sprawdziany muszą być coraz bardziej wytrzymałe i posiadać odpowiednie cechy konstrukcyjne, aby zapewnić prawidłowe zamocowanie części. Muszą one również mieć rozdzielczość i dokładność odpowiednie do pomiaru wymaganych tolerancji. Pneumatyczna technologia pomiarowa coraz częściej staje się rozwiązaniem testowym pierwszego wyboru do sprawdzania tych krytycznych parametrów.
Artykuł napisany przez George'a Schuetza, dyrektora ds. pomiarów precyzyjnych w firmie Mahr Inc.