Formmessung: häufige Probleme verstehen
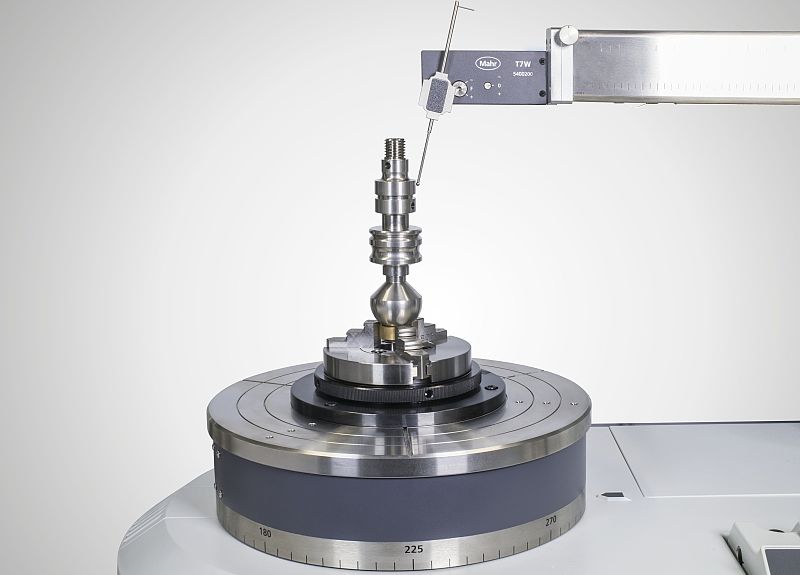
Im einfachsten Fall beinhaltet die Formmessung einen Messtaster und Tastarm mit Tastelement. Dieser wird entlang eines idealen kreisförmigen oder linearen Pfades bewegt, um Daten über die Tasterbewegungen relativ zu dieser idealen Geometrie zu erfassen. Die Analyse ist für gewöhnlich recht überschaubar: Die gemessenen Datenpunkte werden gefiltert und es werden mathematische Operationen daran ausgeführt, um die Ergebnisse zu ermitteln. Obwohl es sich um eine der grundlegendsten Messungen zur Unterstützung vieler Fertigungsprozesse handelt, werden einige Schritte oft fehlerhaft ausgeführt. Besonders häufige Irrtümer entstehen bei der Wahl des Filters und des Tasterelements.
Verwendung falscher Filter
Historisch wurden 50 W/U als Standardwert für Rundheitsmessungen angenommen. Dieser Filter mag zwar für viele Anwendungen geeignet sein, ist aber nicht für alle passend. Die neue DIN EN ISO 1101:2017-09 ermöglicht es, eine geeignete Filtereinstellung direkt mit jeder Formtoleranz in der Zeichnung anzugeben. Nichtsdestotrotz gilt nach wie vor, dass sich die korrekte Wahl des Filters nach der Messaufgabe richten muss. Es liegt in der Verantwortung von Konstruktion, Arbeitsplanung und Qualitätsmanagement, anforderungsbezogene Filtereinstellungen festzulegen, diese in Hausnormen festzuhalten und für alle internen und externen Lieferanten vorzuschreiben.
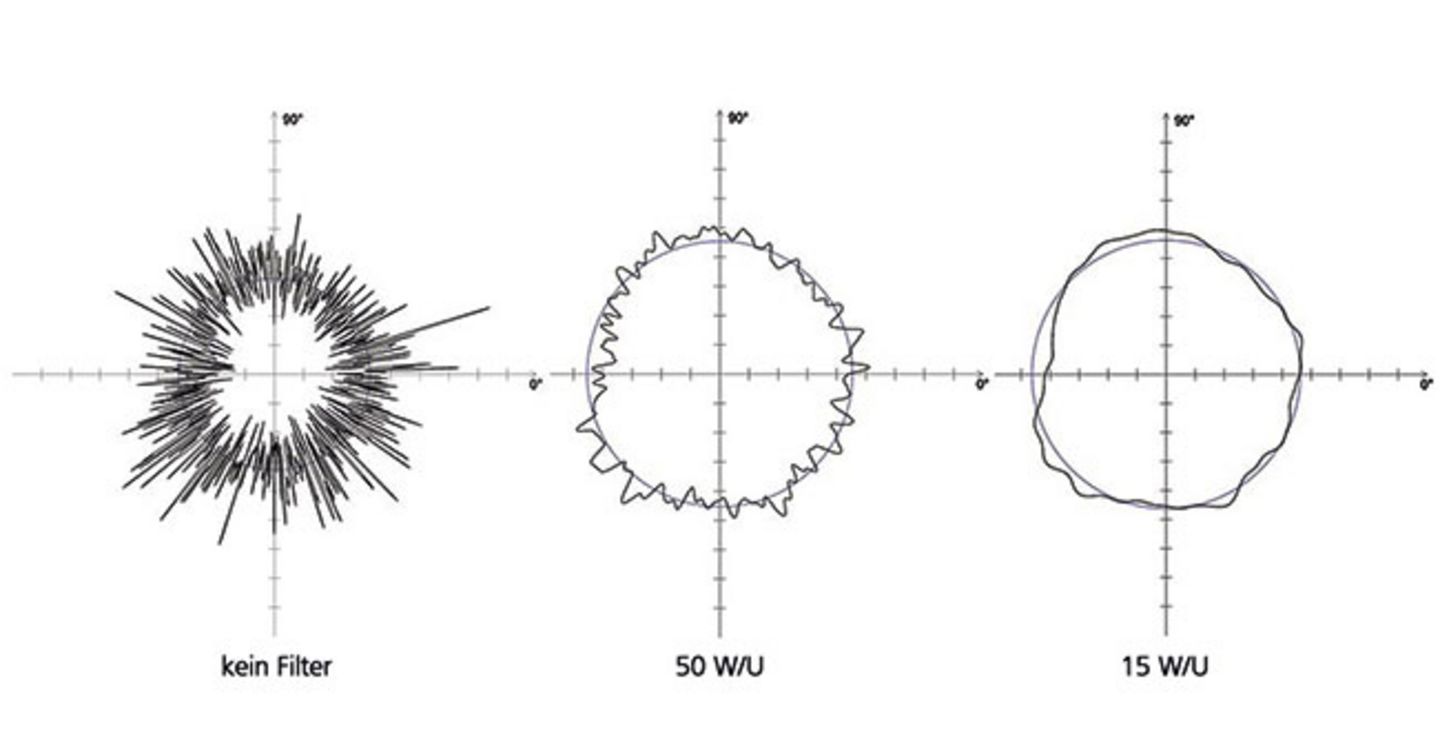
Realistisch betrachtet ist die Formmessung ein Prozess zur Messung von Formabweichungen. Traditionell wird sie in klimatisierten Labors durch hochqualifizierte Spezialisten vorgenommen, doch heutzutage wird sie oftmals direkt in der Fertigung von Mitarbeitern ausgeführt, die mit einem breiten Aufgabenspektrum betraut sind. Egal ob Form- oder Rauheitsmessung: die Vorgangsweise ist im Wesentlichen gleich. Bei jeder beliebigen Oberflächenmessung werden üblicherweise viele Abtastpunkte verwendet, um die gesamte Oberfläche darzustellen. Diese Punkte werden anschließend gefiltert, um nur die gewünschten Daten zu erhalten. Beispielsweise werden bei der Prüfung der Oberflächenrauheit die Daten mit kürzerer Wellenlänge für die Analyse beibehalten, während die formbezogenen Daten verworfen werden, weil diese Information nicht benötigt wird. Dagegen werden bei der Formmessung die Daten mit kurzer Wellenlänge herausgefiltert, um die Daten mit langer Wellenlänge, welche die Form darstellen, messen zu können. Dies ist der erste Punkt, an dem sich bei vielen Anwendern Fehler einschleichen: Die feinen Nuancen der Filterung werden nicht immer ohne weiteres verstanden und daher oft die falschen Filter gewählt.
Die Filter für die Formmessung sind für viele Messtechniker verwirrend. So wird bei der Diskussion der Messung der Oberflächenrauheit beispielsweise von den Filtereinstellungen in Bezug auf Millimeter oder Zoll gesprochen. Wird der Filter auf 0,8 mm eingestellt, versteht man darunter im Allgemeinen, dass Oberflächenabweichungen von weniger als 0,8 mm als Oberflächenrauheit angesehen werden, während Elemente von über 0,8 mm als Formfehler der Oberfläche betrachtet werden.
Formfilter für Rundheitsmessungen werden jedoch meist als Winkelgröße angegeben – anstatt als Länge oder Abstand. Um alles noch verwirrender zu machen, erfolgt die Angabe in den Spezifikationen nicht direkt in Winkelgraden, sondern in einer als ‚Wellen pro Umdrehung‘ oder W/U (engl.: UPR) bezeichneten Einheit. Viele Anwender wählen als typischen Standardwert 50 W/U. Dies bedeutet, dass die Länge des Filters 1/50stel eines Kreises – also 7,2 Grad – beträgt.
Werkstückdurchmesser für die Filterauswahl berücksichtigen
Allerdings ändert sich die Bogenlänge, die 7,2 Grad auf der Oberfläche eines runden Objektes entspricht, mit dem Durchmesser (d) des Objekts. Eine einfache Formel für den Umfang eines Zylinders ist: π * d. Ein Zylinder mit 4 mm Durchmesser hätte also einen Umfang von 12,57 mm – und daher würden 7,2 Grad eine Bogenlänge ausschneiden, die entlang der Oberfläche 0,25 mm misst. Ist hingegen ein Zylinder mit einem Durchmesser von 20 mm zu messen, würde dieser einen Umfang von 62,83 mm aufweisen und den 7,2 Grad würde eine Bogenlänge von 1,26 mm entsprechen. Wenn also dieselbe 50 W/U Filtereinstellung am Messgerät beibehalten wird, werden im Fall des größeren Teils fünfmal größere Oberflächenabweichungen als Grenze zwischen den Merkmalen Form und Oberflächenrauheit berücksichtigt. Bei quasi allen Messgeräten lässt sich die Filtereinstellung ganz einfach durch Anklicken einer Schaltfläche in der Software ändern — jedoch verstehen viele die Bedeutung von W/U (UPR) nicht und ändern die Voreinstellungen daher nicht.
Auch das Gegenteil ist manchmal der Fall: fehlt das Verständnis dafür, dass die Filtereinstellung einen deutlichen Einfluss darauf hat, was von den Daten herausgefiltert oder für die Analyse beibehalten wird, könnten Messtechniker versucht sein eine andere Einstellung zu wählen. Ein abweichender Wert würde die Ergebnisse jedoch verändern und so zu einem Resultat führen, dass zwar „besser aussieht“, aber nicht wirklich korrekt für die Größe des Prüflings ist. Die Quintessenz ist, dass der Filter korrekt für das jeweilige Messobjekt eingestellt werden sollte.
Falsche Größe des Tastelements
Ein zweiter, weit verbreiteter Fehler ist, dass Anwender sich auf eine einzige Tastelementgröße zur Messung aller Teile verlassen, ungeachtet der Größe des Prüflings. Tatsächlich stellt die Tastkugel des Tastelements selbst einen mechanischen Filter dar, der entsprechend der Werkstückgröße und der maximal messbaren Anzahl von Wellen pro Umdrehung gewählt werden sollte.
Am Beispiel eines kleinen Bauteils mit einem Durchmesser von 4 mm kann das Problem anschaulich geschildert werden: Wird die Messfläche mit einem Taster mit zu großem Tastelement abgetastet, kann dieser nicht gut entlang der Oberfläche laufen und präzise den Aufs und Abs der Spitzen und Täler folgen. Werden auf einem Taster Tastelemente verwendet, die sich der Größe des Werkstückdurchmessers selbst annähern, wird es sehr schwierig, eine gute Bewertung der Oberfläche zu erhalten. In diesem Fall bewirkt die Verwendung dieses Tastelements eine mechanische Filterung – noch bevor irgendeine mathematische Filterung erfolgt. Die VDI/VDE 2631 Blatt 3 gibt dem Anwender einen Leitfaden zur Auswahl des korrekten Tastelements auf Grundlage der W/U-Einstellungen, der maximal zu erwartenden Einzelwellentiefe und des Prüflingsdurchmessers.
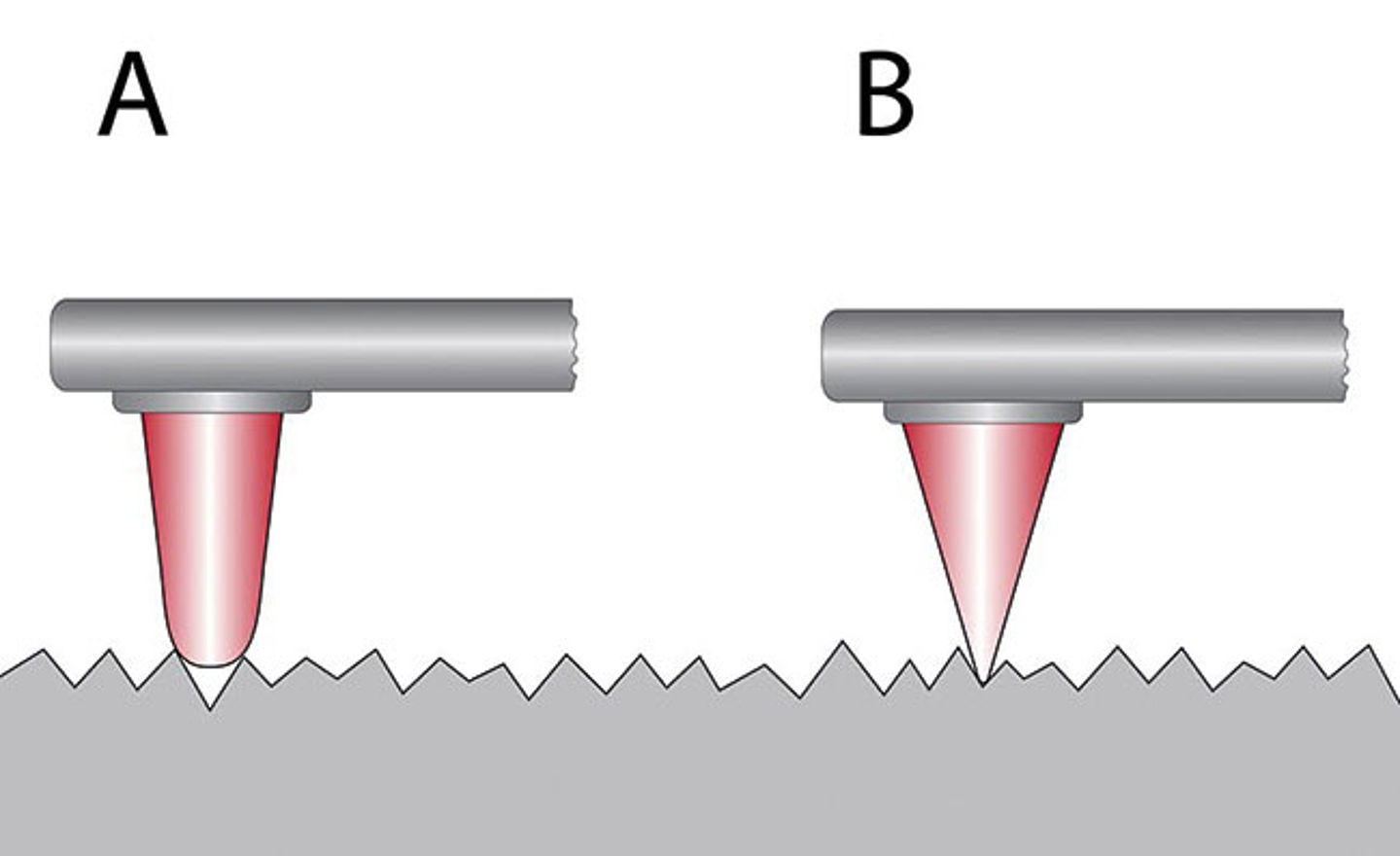
Schlussfolgerung
Obwohl die Formmessung eine der Grundaufgaben zur Unterstützung zahlreicher Fertigungsprozesse darstellt, führen viele Anwender einige Aspekte davon häufig fehlerhaft aus. Hierdurch kann sowohl die Güte der Messungen als auch die Gesamtqualität des Endprodukts beeinträchtigt werden. Durch die Einhaltung einiger grundlegenden Schritte, wie die korrekte Anwendung der für die jeweilige Situation geeignetsten Filter und die Ermittlung der richtigen Daten für den jeweiligen Anwendungsfall, kann ein exaktes Ergebnis sichergestellt werden. Auch der Einsatz des bestpassendsten Zubehörs, wie beispielsweise genau für die Anwendung bemessene Tastkugeln, bringt den Nutzer ein gutes Stück voran in Richtung einer verbesserten Messdatenqualität - und damit letztendlich einer höheren Werkstückqualität.